``Li3-Method presents a planning concept to generate complex facade and building envelopes that can be constructed by applying standard mullion-transom facade systems. The mullion-transom system combined with N-AM_Li3 node (European Patent No. EP4051843) can be constructed as a stick system, unitized system, or free-form shell strucutre, in either steel or aluminium`` Mohsen, Alamir. Design to Manufacture of Complex Building Envelopes: Single Layer Envelopes: Mullion-Transom Systems+ 3D Printed Metal Nodes. Vol. 56. Springer Nature, 2020.
LinkLi3-Method
Li3M Software
N-AM_Li3
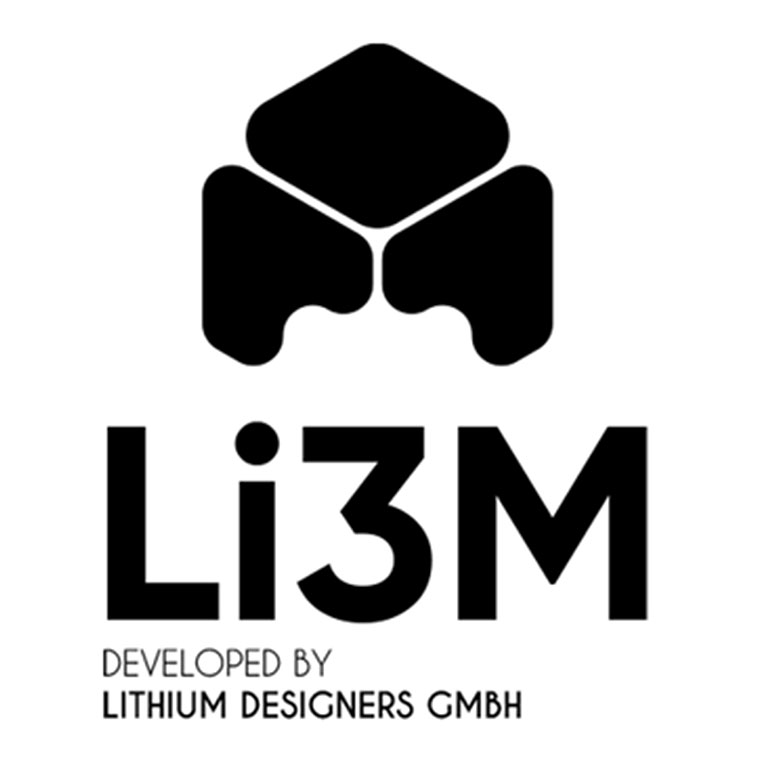
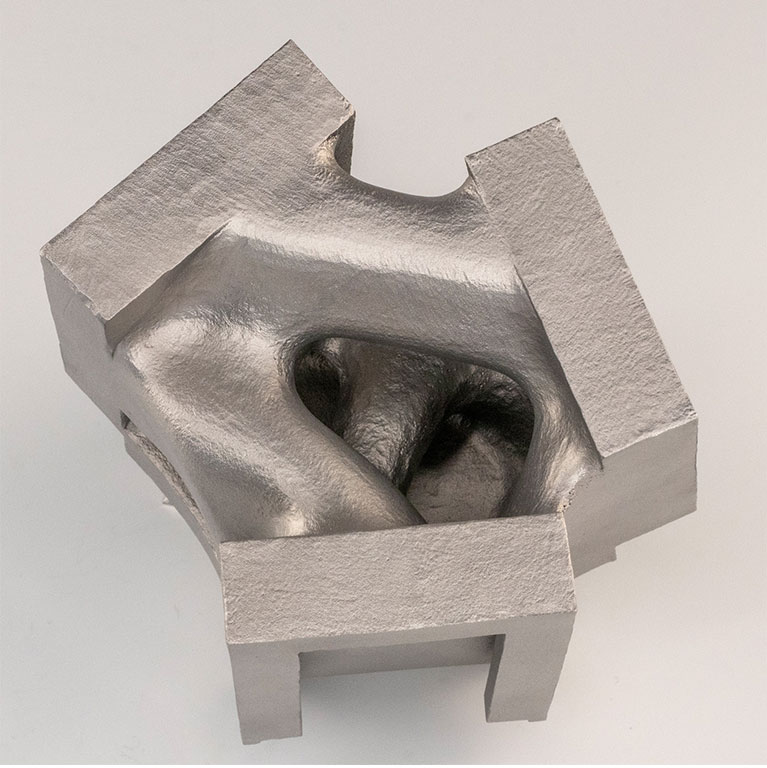
Li3M is an innovative, fully digital planning software developed by Lithium Designers for the design, structural analysis, and manufacturing of complex freeform facades and building envelopes. It enables the parametric modeling of geometrically complex structures, automatically generates topology-optimized nodes (N-AM_Li3) using ANSYS simulations, and seamlessly integrates with RFEM for static calculations. These 3D-printed nodes, produced via selective laser melting, are directly exportable from Li3M as CAD files and sent to manufacturing partners. By combining standard profile systems with digitally generated connectors, Li3M transforms traditional facade construction into a streamlined, cost-efficient process, significantly reducing planning effort, material waste, and construction time
The N-AM_Li3 nodes are topology-optimized, 3D-printed metal connectors developed by Lithium Designers as part of the Li3_Method for constructing freeform facades and building envelopes. Each node is uniquely generated through structural simulations in ANSYS to ensure that only the material necessary for load-bearing performance remains, resulting in lightweight, bionic geometries that are both functional and aesthetically distinct. Manufactured via selective laser melting in aluminum or steel, these nodes integrate seamlessly with standard mullion-transom systems and enable a modular “Lego-like” assembly process without welding. This innovation allows for faster, more precise, and cost-effective realization of complex architectural designs while reducing material waste and simplifying on-site construction
Projects & Concepts
N-AM_Li3 1st Gen. (Concept, developed in 2013)
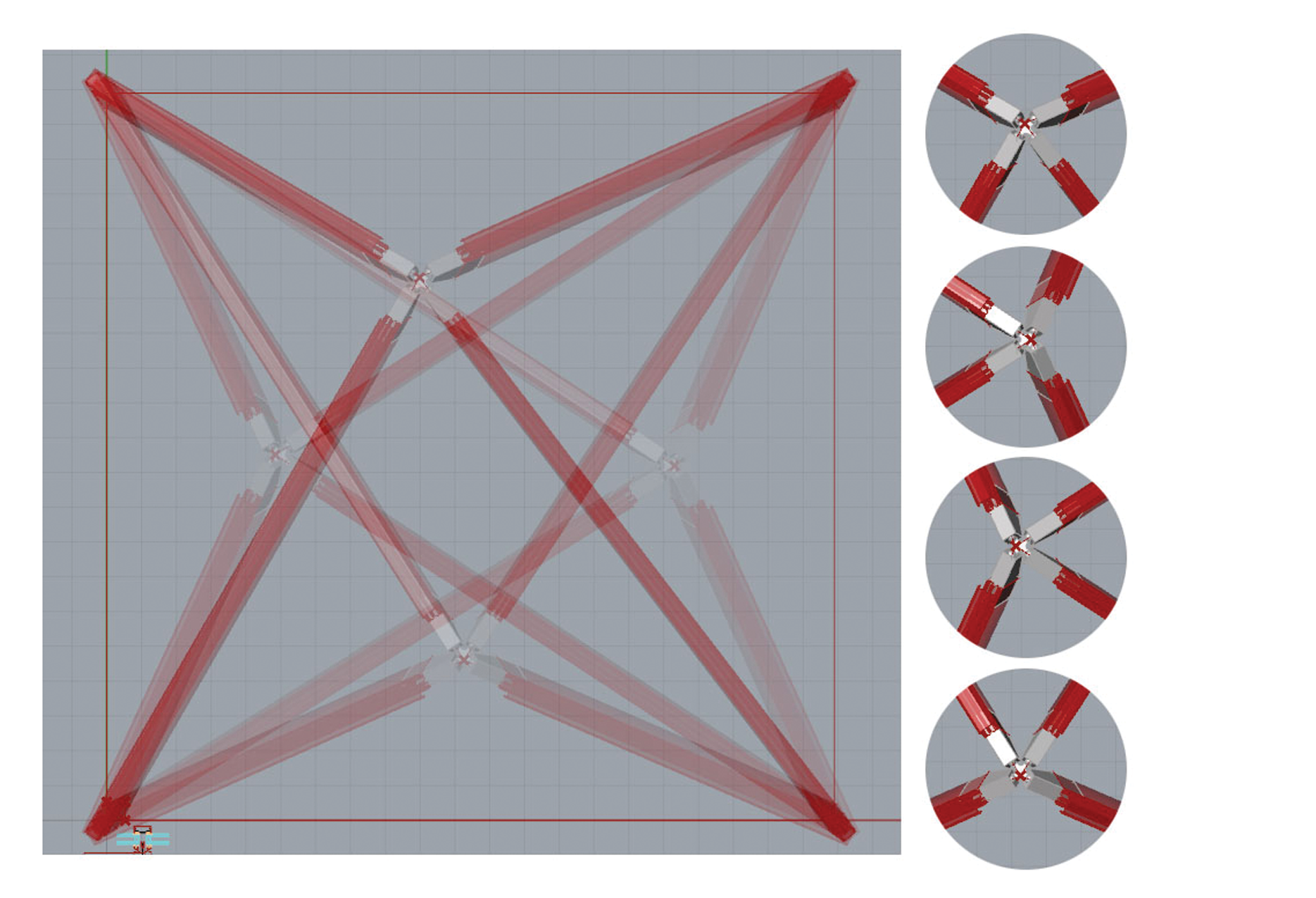
In the early phase of research, the focus was on integrating parametric modeling into the design process, without yet considering additive manufacturing. The concept centered around using a spherical ball connection within the node to allow full rotational freedom along all axes, accommodating various profile orientations. These early designs, known as the N-AM series, were digitally modeled and optimized to align with connecting profiles, determine their normal vectors, and position the node efficiently. The first generation of N-AM successfully demonstrated the flexibility to parametrize complex façade units and generate the necessary data for manufacturing and assembly. This success led to the decision to fully digitalize the node and explore additive manufacturing, advancing toward highrise-tessellation and grid shell formation on freeform surfaces.
N-AM_Li3 2nd Gen. (Concept, developed in 2015)
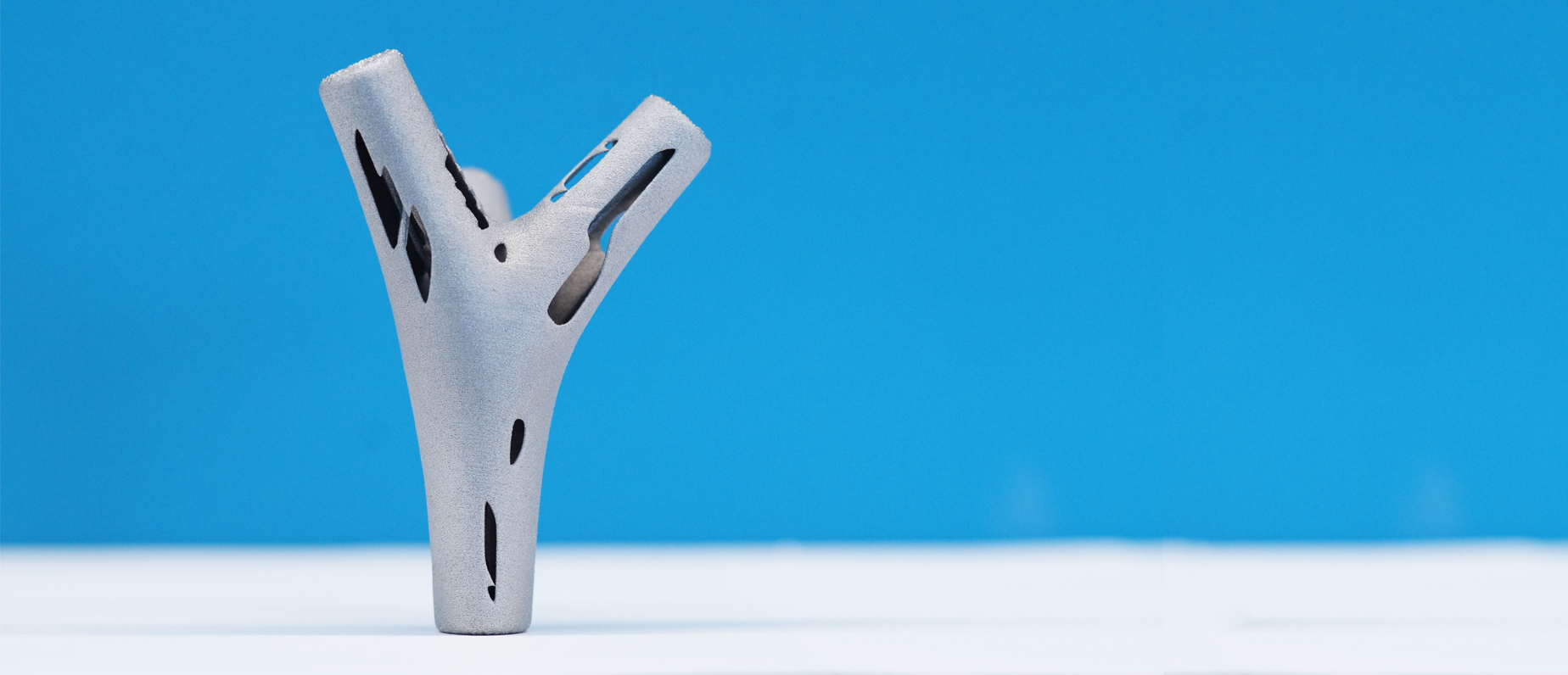
The N-AM 2nd Generation built on the success of the first iteration by addressing limitations in accommodating only regular geometries. Its development focused on creating a fully integrated parametric workflow using Grasshopper and Rhinoceros. This workflow included node generation based on structural position, structural analysis, mesh relaxation for shape optimization, and stress-based topology optimization. The prototype, known as N-AM 10, featured four round hollow profiles converging at a point and was refined using Kangaroo for mesh relaxation and Karamba for structural analysis. Topology optimization, based on SIMP methodology, was applied to remove low-stress mesh cells and reduce material usage. The resulting stainless-steel node was manufactured using the EOSINT M270 system, demonstrating the feasibility of a fully digital, single-step process, though physical testing was not yet performed.
N-AM_Li3 (Concept, Released in 2019)
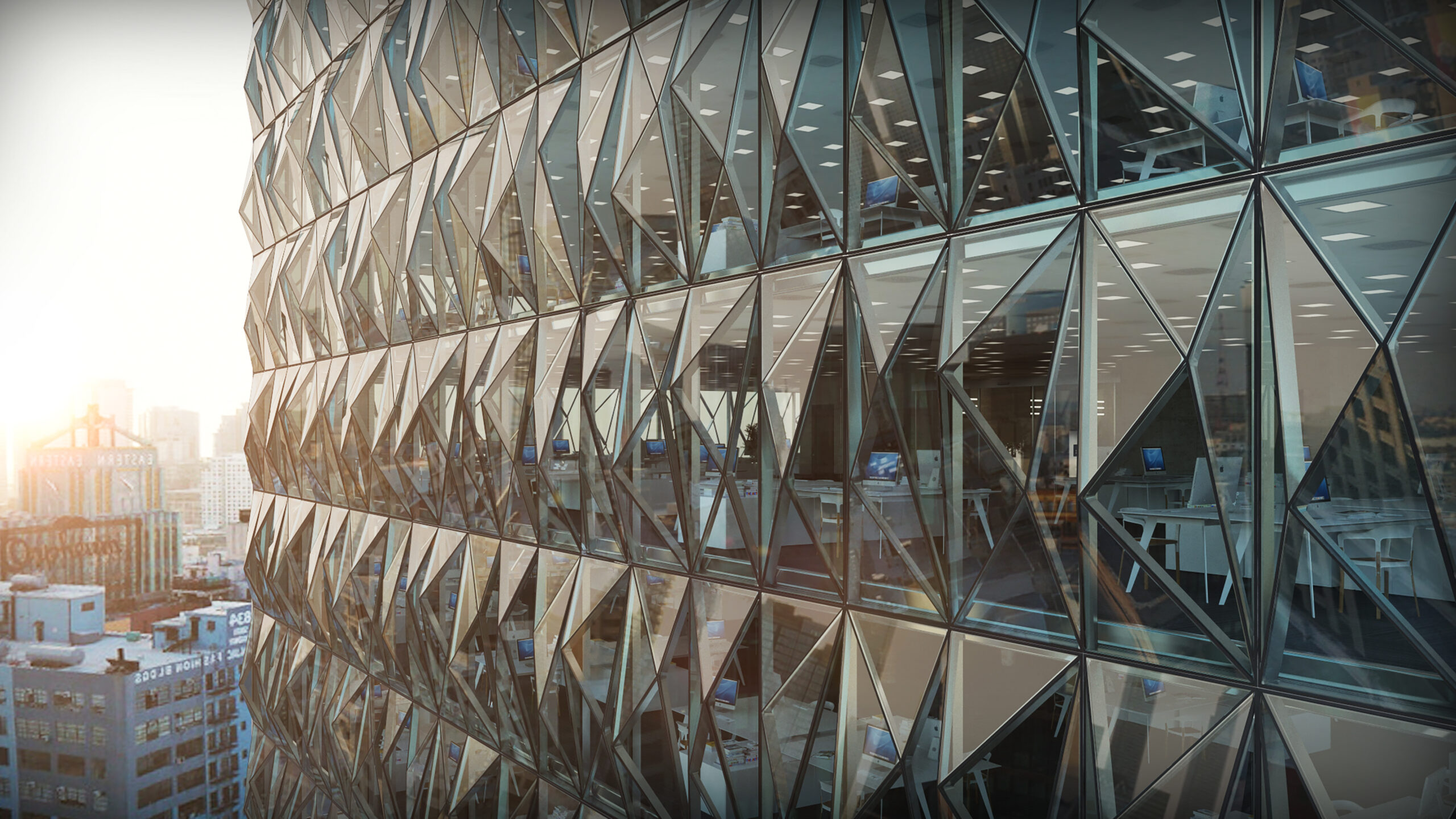
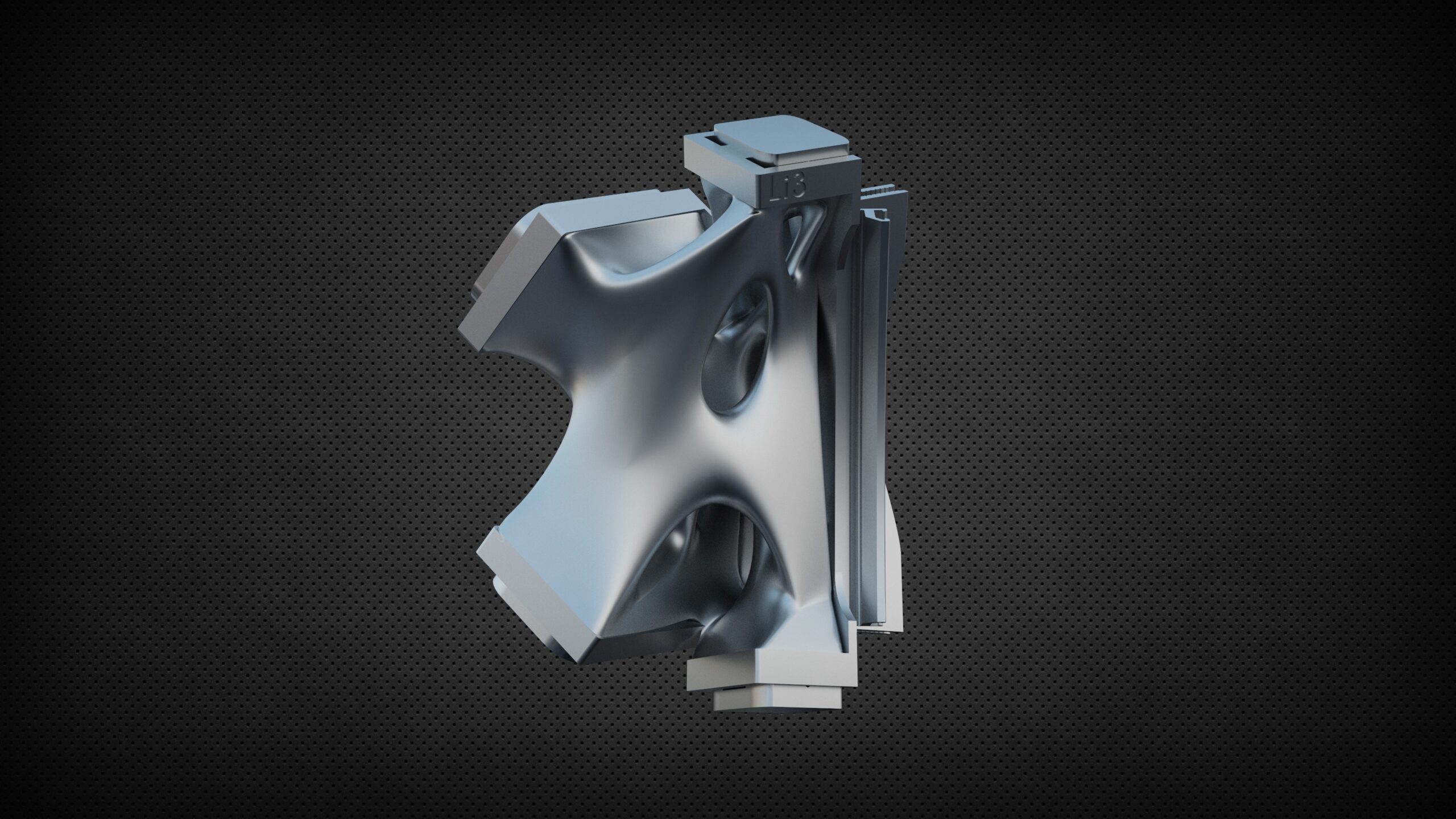
N-AM_Li3 represents the first fully validated, testable version of our 3D-printed facade node, developed to transition from prototype to product. Designed using a fully integrated digital workflow—combining parametric modeling, structural simulation, and topology optimization—the node was engineered for aluminum (AlSi10Mg) and manufactured with a RENISHAW metal 3D printer. Various connection strategies were explored, with the final version featuring a sliding dovetail connection fixed by two screws through the drainage channels, ensuring structural rigidity and alignment with facade profiles. The node’s form was optimized for additive manufacturing, minimizing support material and maximizing stiffness while maintaining a compact build volume. A comprehensive component test validated its structural integrity, confirming failure at approximately 6 mm displacement under a load of 63 kN. This milestone proves the effectiveness of our Li3_Method and establishes N-AM_Li3 as a structurally sound, digitally fabricated connector for freeform facades.
HivE (Project, completed in 2022)
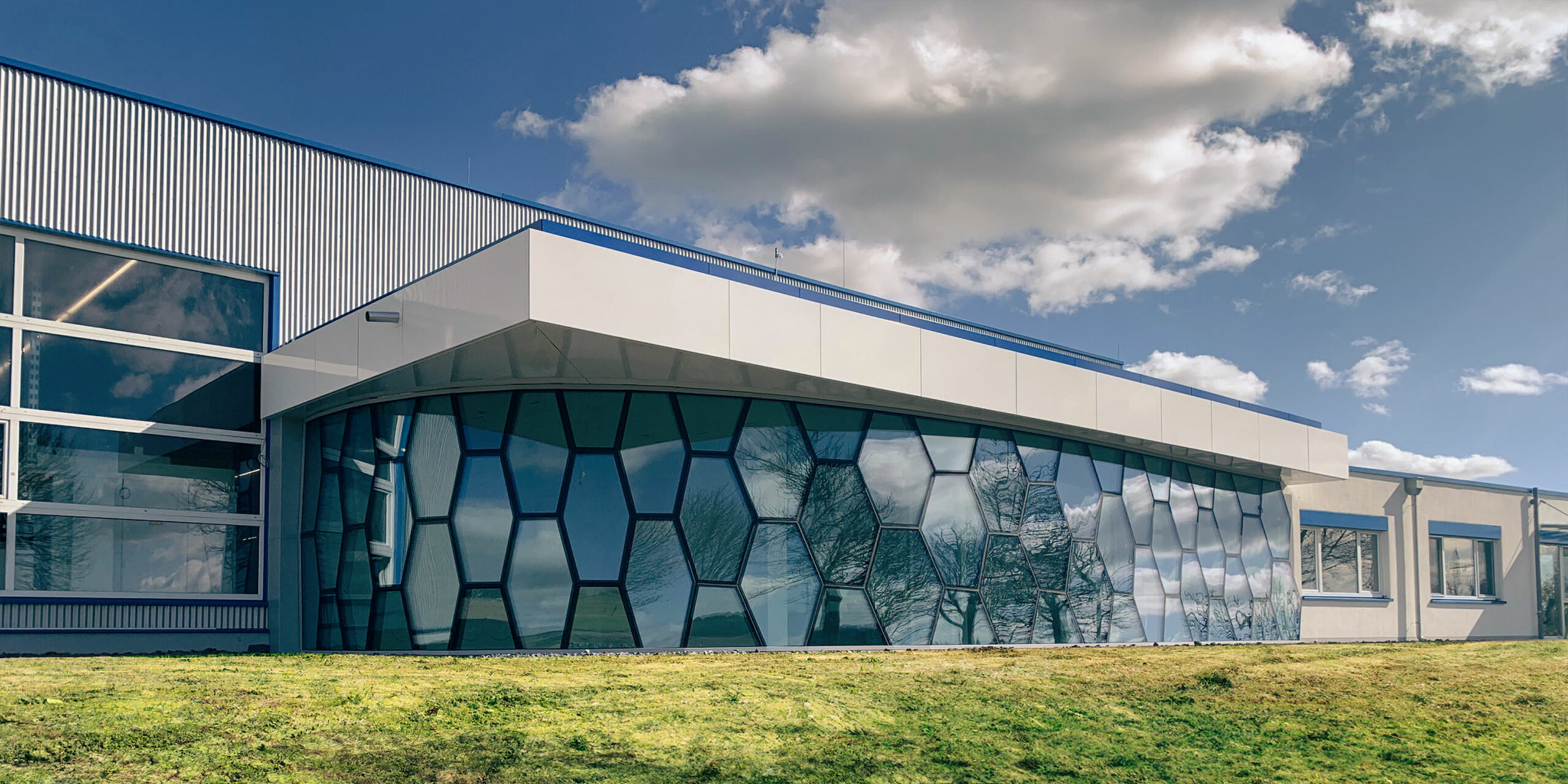
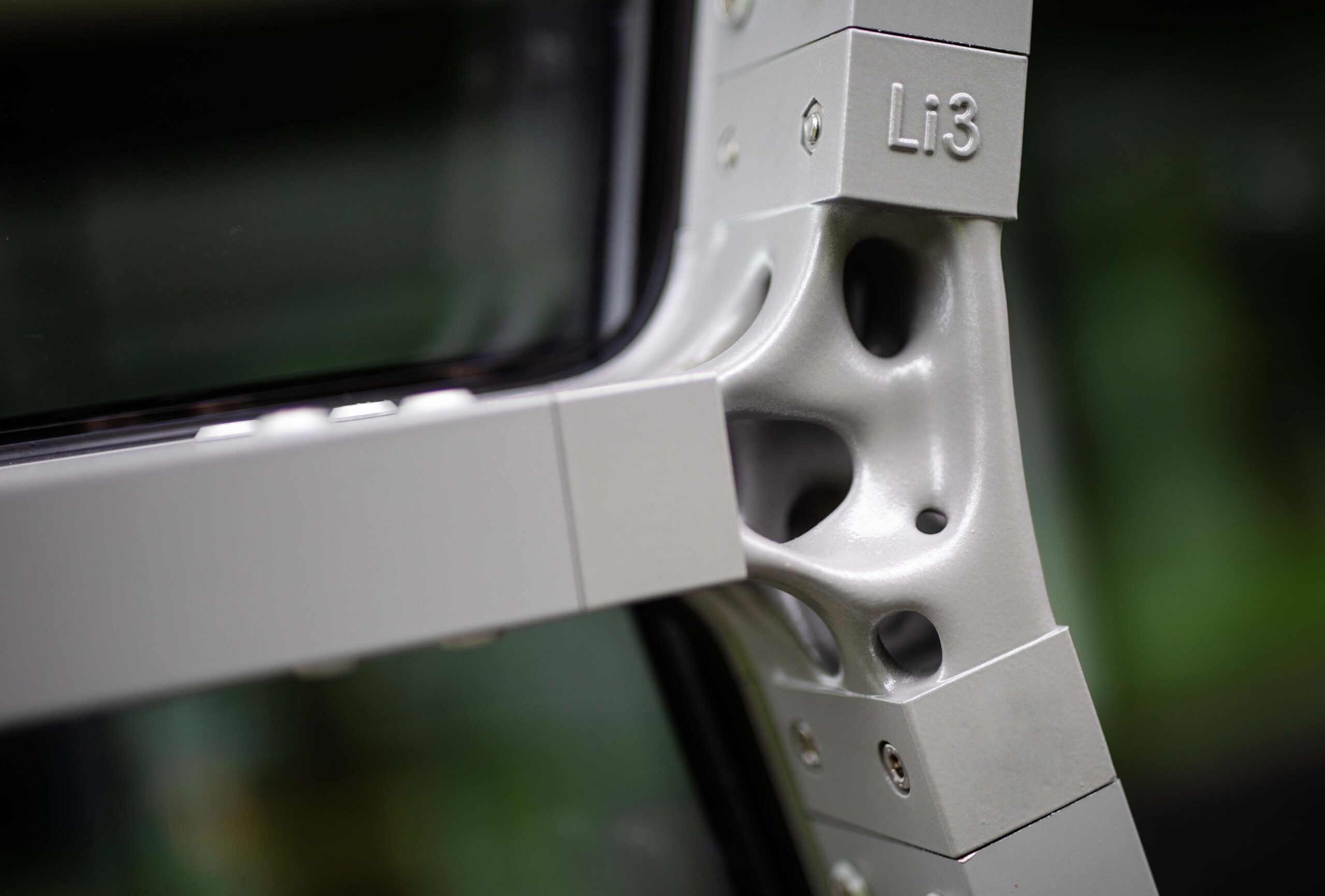
HivE is the world’s first architectural project to implement 3D-printed metal nodes in a real building facade, showcasing the full potential of Lithium Designers’ Li3_Method. Completed in collaboration with an automobile company in Adelmannsfelden, the project features a freeform glass facade composed of 134 uniquely shaped N-AM_Li3 nodes, produced using selective laser melting and assembled in just eight hours without welding. Using the in-house planning software Li3M, the entire facade was digitally designed, structurally calculated, and prepared for production, achieving a seamless integration of Schüco’s FW50 SG.Si system with triple-glazed insulation glass. HivE received special approval (ZiE) from the state of Baden-Württemberg and won multiple awards, including the 3D Pioneers Challenge 2021 and the ICONIC AWARDS 2022, establishing Lithium Designers as a global pioneer in digital and additive construction technologies
The N-AM_Li3 nodes used in the HivE project were 3D-printed from aluminum alloy using selective laser melting and served as the core structural connectors within the freeform glass facade. Designed to integrate with the Schüco FW50 SG.Si system, the nodes featured a visible screw connection to the aluminum profiles, enabling a stiff and secure attachment without the need for welding. Three distinct types of nodes were developed to accommodate the specific structural roles within the facade: upper support nodes, lower support nodes, and free nodes. Each node was uniquely generated through parametric modeling and structural optimization, ensuring both functional performance and architectural precision. This custom, performance-driven approach enabled the efficient realization of complex geometry with minimal assembly effort on site.
Westfield Hamburg-Überseequartier (Project, completed in 2025)
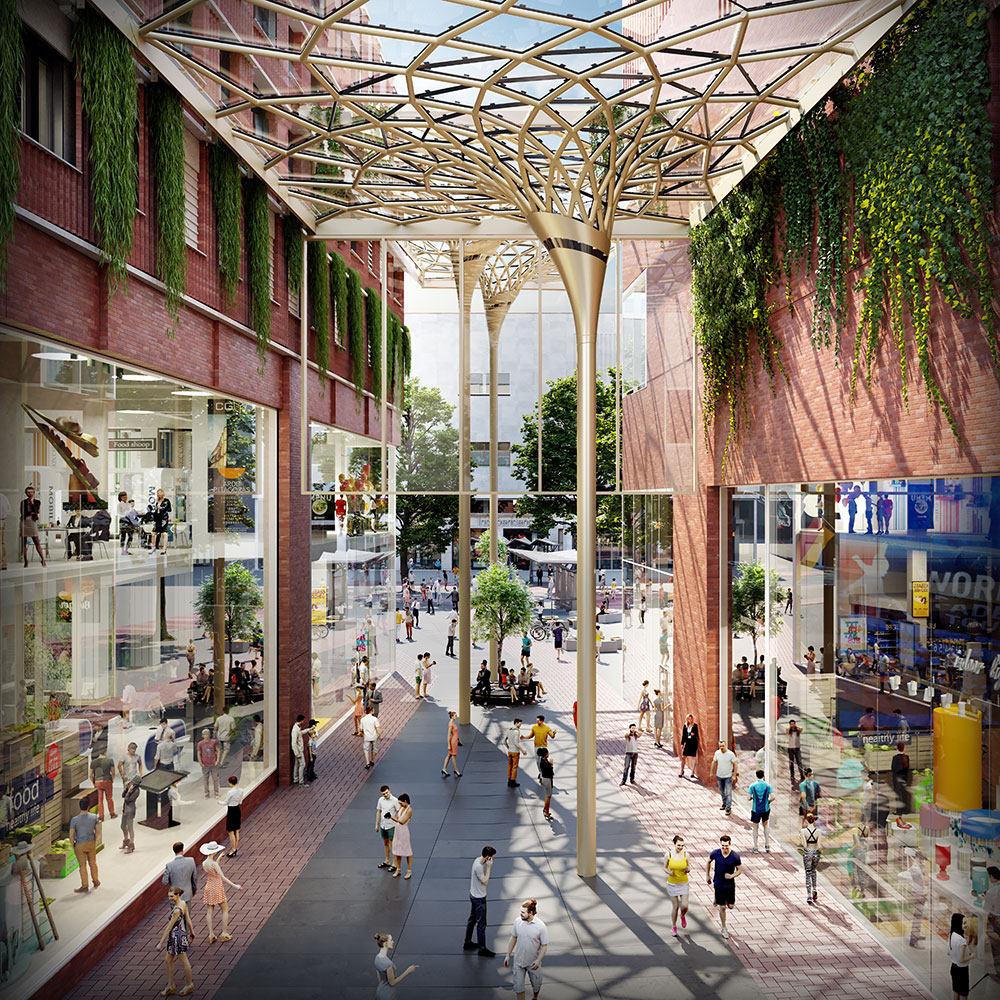
Located in the heart of Hamburg’s HafenCity, the Westfield Hamburg-Überseequartier is Europe’s largest inner-city development project, featuring a spectacular metal and glass roof designed by Werner Sobek. This delicate mesh of steel and glass spans large sections of the district, significantly enhancing the public space and creating a weather-protected, open-air experience for shopping and leisure. The project marks the first large-scale implementation of our Li3_Method, proving its feasibility in complex architectural applications. The roof comprises approximately 20,000 unique profiles, 9,700 CNC-milled nodes—4,350 in aluminum and 4,350 in steel—and 8,353 individual glass panels. Each of the 34 supporting columns features a unique geometry derived from its position within the structure. Through a highly precise digital planning and optimization process, a high degree of standardization for profiles and glass panes was achieved—despite the complexity of the freeform geometry.
LucID (Concept, released in 2023)
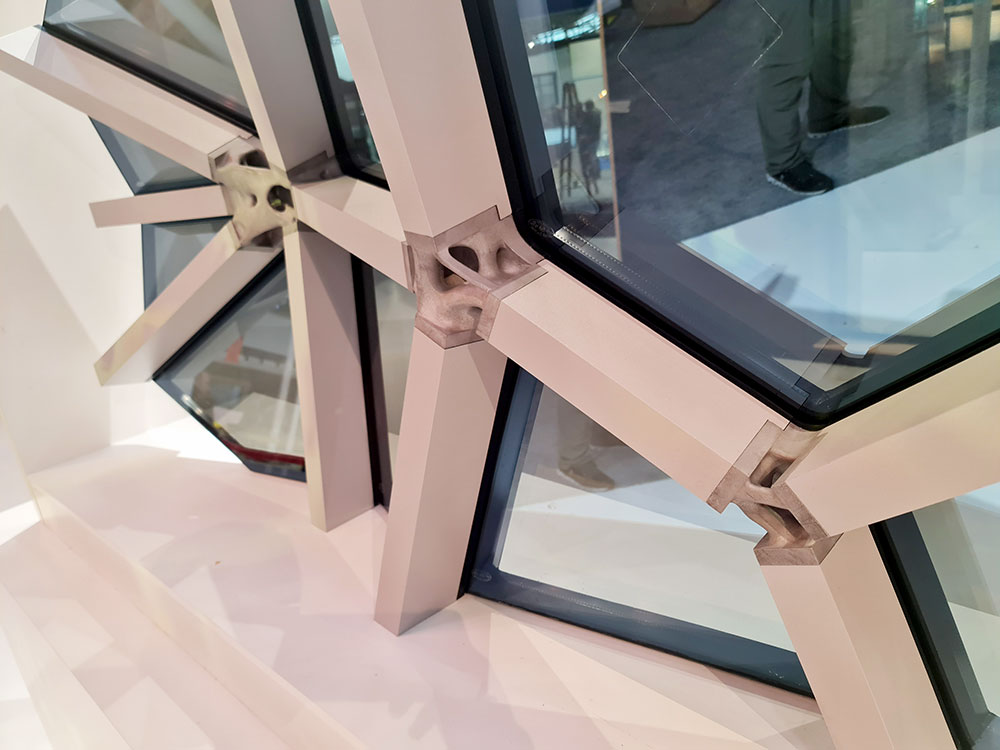
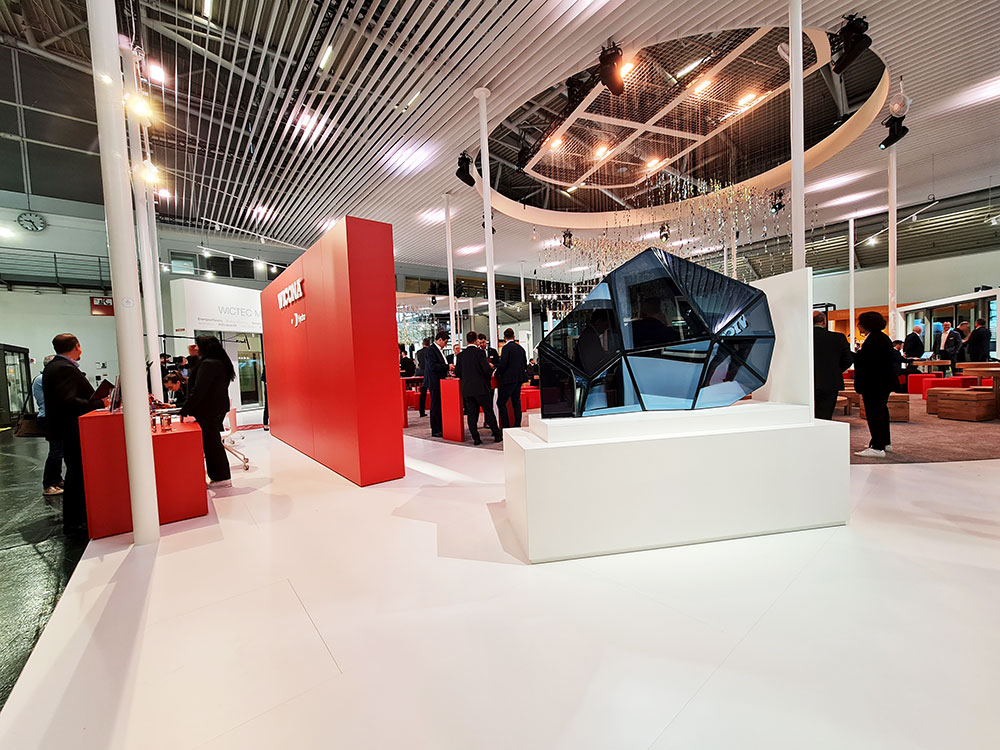
Unveiled in 2023 at BAU Messe in collaboration with Hydro Building Systems, LucID represents the next evolution of our node technology. This upgraded series introduced three node types—3-arm, 4-arm, and 6-arm—demonstrated through a full-scale mock-up. LucID features a newly engineered slim-profile connection that significantly enhances structural strength while maintaining a minimal visual footprint. Compared to earlier versions, the refined connection design offers improved mechanical performance and seamless integration into standard facade systems, setting a new benchmark for elegant and robust freeform construction.
HarMoniE – (Nursing Home Concept in Walldorf, Germany, developed in 2023)

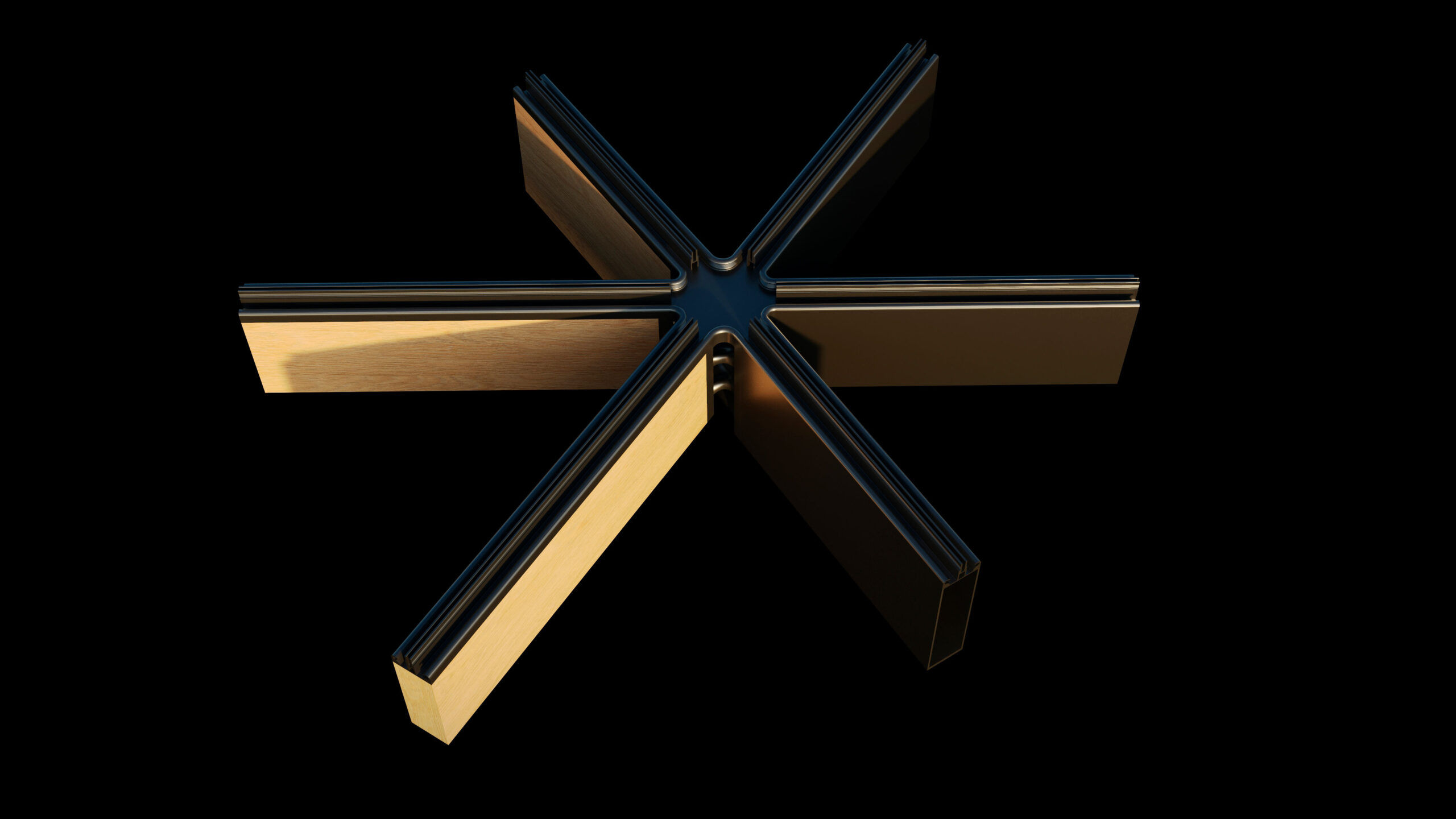
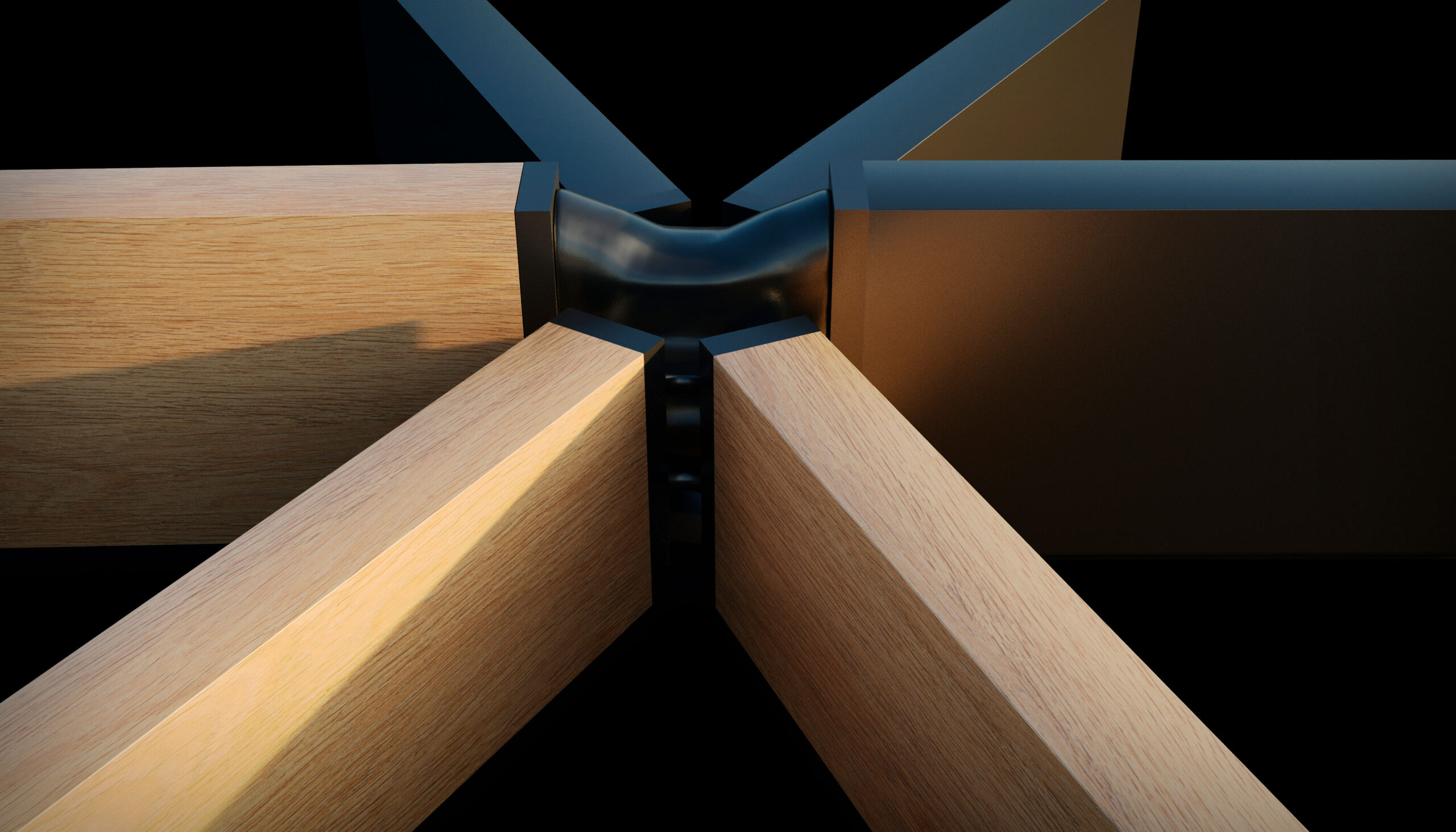
As part of a design competition, Lithium Designers proposed the nursing home “HarMoniE” as an architectural bridge between past and future. The building is composed of three wings connected by daylight-filled stairwells and a central atrium—spaces designed to foster connection, memory, and orientation. The facade merges natural wood with modern metal elements, symbolizing the harmony of tradition and innovation. Three freeform roof domes serve as green urban oases while enhancing natural lighting, ventilation, and solar energy collection. The entire structure is based on a sustainable timber-panel construction, combining ecological responsibility with architectural clarity.
3D-Printed Nodes – Where Geometry Meets Sustainability
At the core of the proposal was the use of 3D-printed nodes to connect the complex geometry of the roof domes. These nodes were parametrically designed, topology-optimized, and additively manufactured to meet both architectural and structural demands. Connecting timber and aluminum profiles in a mullion-transom system, the nodes demonstrated the practical application of the Li3_Method in a healthcare architecture context. While the project was not selected for realization, it showcases how digital planning and sustainable fabrication can lead to innovative solutions in social and healthcare design.
VinEyaRd – (Town Hall and “Bären” Site Concept in Durbach, Germany, developed in 2023)
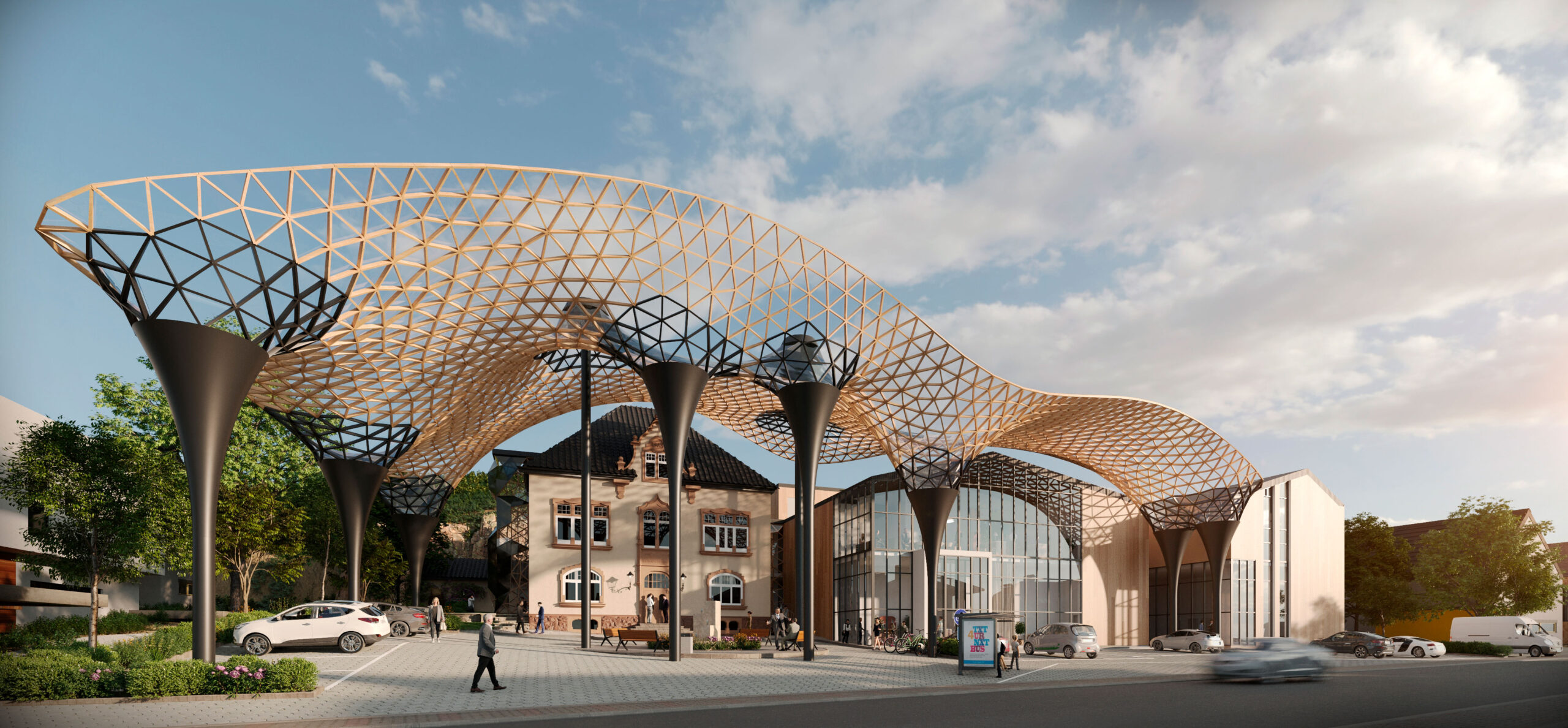
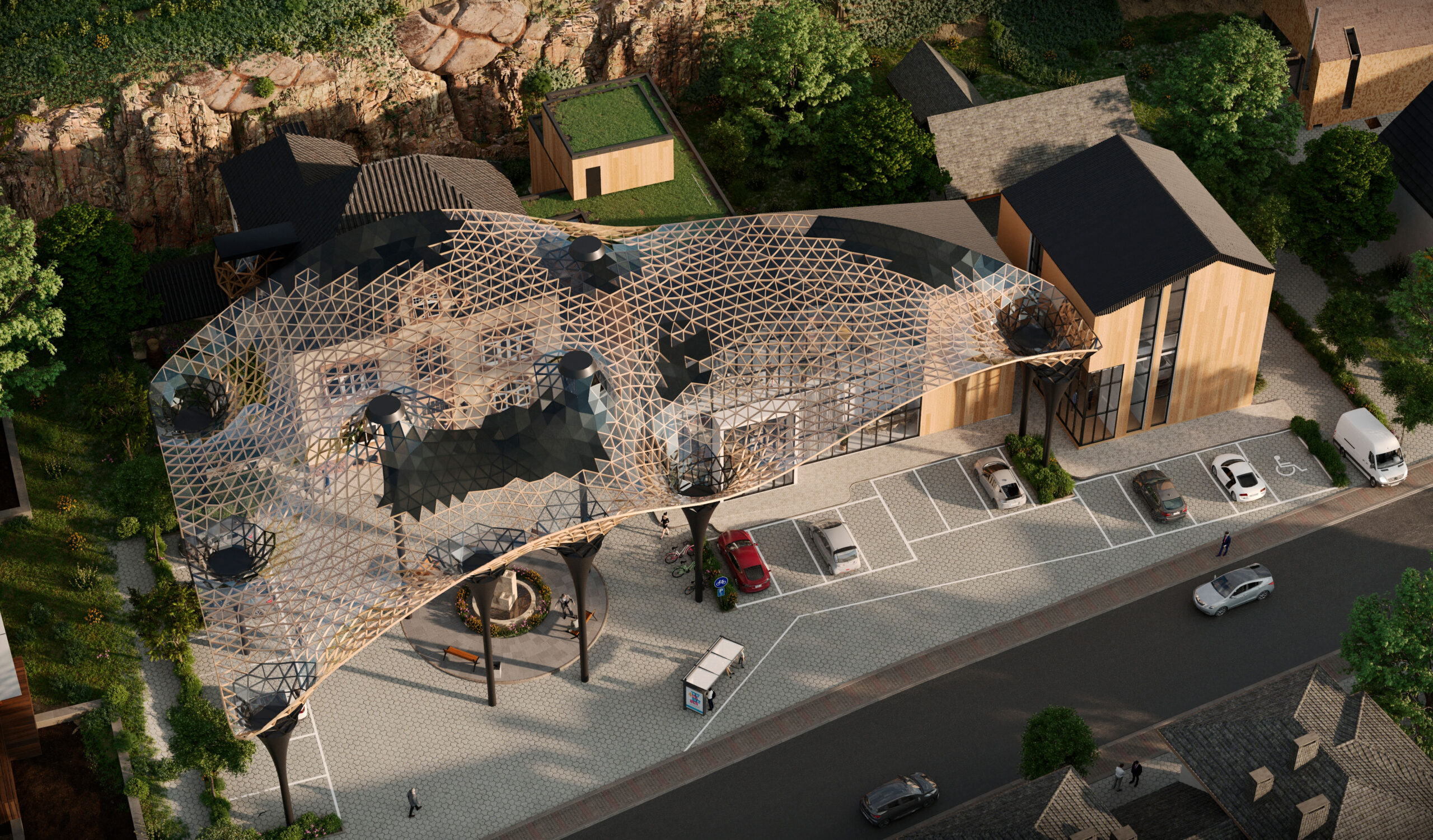
Set in the picturesque landscape of Durbach, Germany, VinEyaRd is a visionary concept that merges architectural elegance with the surrounding natural beauty. Inspired by the flowing topography of the region’s vineyards, the design features a striking freeform glass roof that crowns a new town hall extension and the redesigned “Bären” building. The new structures are connected by an elegant bridge and strategically positioned to form a welcoming public square. Natural materials—wood, recycled aluminum, and glass—define the character of the building, while sustainable timber panel construction ensures ecological performance. The transparent corner of the extension opens the space to daylight and views, and the entire complex includes civic functions, a restaurant, and apartments—blending public life, hospitality, and living into a cohesive architectural ensemble.
Topology-Optimized Nodes for Freeform Architecture
A central architectural and structural highlight of VinEyaRd is its expressive glass roof, shaped to follow the soft curves of the Durbach hills. The roof is supported by a hybrid system of wood and recycled aluminum profiles, precisely connected by topology-optimized, 3D-printed nodes. These custom-designed nodes serve as the invisible yet essential components enabling the realization of the freeform geometry. Their fabrication through additive manufacturing allows for maximum precision, minimal material waste, and a strong commitment to sustainability. As a design proposal, the project demonstrates how advanced digital planning methods and smart material strategies can shape meaningful, place-specific architecture.
Stay tuned for our upcoming projects!